Student-led project aims to improve productivity, working conditions at a medical device company
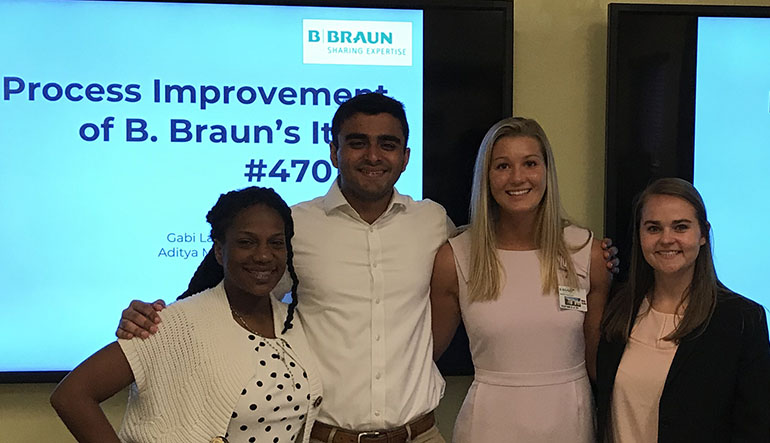
Aditya Mehta ’18 (second from left), Gabrielle Lassinger ’18 (second from right), and Colleen McGovern ’18 (far right) visited B. Braun’s Santo Domingo plant to deliver operations recommendations.
By Bryan Hay
A group of senior chemical engineering majors and their advisers recently returned from a whirlwind trip to the Dominican Republic where they presented their findings to improve operations and working conditions at a medical device manufacturing plant.
Since last semester, Visiting Assistant Professor Alex Woltornist’s senior design class in chemical engineering — Colleen McGovern ’18, Gabrielle Lassinger ’18,, Aditya Mehta ’18, and Ugochukwu Okeibunor ’18 — following an initial visit to B. Braun Medical Inc.’s Allentown, Pa., site, has been meeting regularly via Skype with the operating team at a plant in Santo Domingo about how to optimize assembly of small bore extension sets and improve the ergonomics of manual work for employees.
Braun, a global medical device company, is a leading manufacturer of extension sets, which are connected to IV catheters to eliminate the need for additional lines to administer fluids.
Students had three goals: increase manufacturing capacity at the facility and reduce costs, further improve quality built into the product, and improve the work for assembly-line employees who make millions of extension sets every year.
McGovern said they observed GoPro videos, which showed how line workers assemble the extension sets in varying batches. Their recommendation, based on trials and data, is to produce in single piece flow, one assembly at a time, instead of making four to eight assemblies at one time.
“We found it was faster and more efficient to assemble one set at a time,” McGovern said. That recommendation, along with others related to work balance and parts presentation, has the potential to significantly cut assembly time and increase capacity by reducing labor hours for manufacturing.
To improve the comfort of employees, students recommended adjusting the height of the bin used to collect finished extension sets and installing a miniature conveyor to move fully assembled units.
Woltornist said B. Braun valued the recommendations, which were presented to the site Leadership Team by the students at the Santo Domingo plant on May 3.
“They valued the different perspective because often you’re too close to something and don’t see the opportunities,” said Woltornist, who also works as a consultant for B. Braun and introduced the Lafayette students to the company. “The students brought a fresh set of eyes and challenged everything, which is what an engineer should do.”
He said each of the students followed a logical thinking process, observed and talked to people to build data, and gain an understanding of gaps in the manufacturing process.
“Once they saw a gap, they sought a way to fix it by testing their hypothesis in a lab at Lafayette to prove it,” said Woltornist, who credits Associate Professor Lauren Anderson, head of chemical and biomolecular engineering, for her leadership in supporting the project and final report-out site visit. “They didn’t jump to conclusions.”
“Working with Lafayette student teams has been rewarding since we are helping develop young engineers by giving them some exposure to real-world problems and global cultures, and in our special case, from a remote location,” said Dave Cardona, manager of technical services engineering at B. Braun’s Santo Domingo plant.
“The experience was also valuable because we got some great recommendations that force us to look at our processes differently, a fresh perspective that challenges our current approaches,” he added. “We expect to be able to use some of the recommendations presented by the team.”
Mehta said B. Braun’s management was very receptive of the findings.
“It was a fresh lens for them,” he said. “They were happy with our results, which were very qualitative and supported by analysis and data.”
Lassinger said she was touched by a veteran worker at B. Braun who said the students taught her so much. “I felt that they were proud of us,” she said.
“Their dedication and excellence surpassed the expectations of all the staff of B. Braun Dominican Republic,” said Karilyn Ruiz, operational excellence senior leader at B. Braun’s Santo Domingo facility. “The robustness of the studies carried out and the ideas shown gave us out-of-the-box problem-solving. The students’ findings are going to be evaluated for implementation in the applicable areas.”
“B. Braun shows a commitment to making things better for patients, and that’s something we found to be very motivational,” McGovern said. “Collaborating with leadership team members more than 1,500 miles away taught me the importance of effective and efficient communication while also illuminating the challenges associated with it.
“It was really neat to see our project come into fruition,” she added. “It was our last assignment of the semester and a perfect way to cap off our chemical engineering curriculum here at Lafayette.”
Before they returned to Easton the evening of May 4, students joined Anderson and Woltornist in some community service by helping cement and paint a B. Braun employee’s home damaged during last year’s hurricane season.
“The kindness and humility shown by the Lafayette students and representatives to the family is priceless,” Ruiz said. “The genuine enthusiasm to help was something remarkable for the lives of those being helped.”
“B. Braun has been a good supporter of Lafayette for the last couple years,” Woltornist said. “We wanted to give something back.”