Custom made implants for humans may be a distinct possibility in the near future, and Benjamin Partlow ’03 (Ludlow, Ver.), a junior double major in mechanical engineering and psychology, is taking part in making that a reality.
Partlow is collaborating as an EXCEL Scholar with Scott Hummel, assistant professor of mechanical engineering.
“The EXCEL project I’m working on is based on a new manufacturing technique, termed Laser Engineered Net Shaping,” says Partlow. “This process uses a high-powered laser and powdered metal to build ‘near’ net shape parts.”
“Imagine a thin laser beam, about twice the diameter of a hair, aimed at a block of steel,” explains Hummel. “The laser heats the steel to a point where it is molten. Powdered metal is injected into the area. Some of it lands in the molten pool of metal and when it does, it melts as well. The laser is moving across the block of steel and the powdered metal is melting, then re-solidifying.”
Hummel likens this process to dipping a candle in a bath of hot wax in that each time the process is repeated, it grows a bit more.
“The benefits of this method are that it does not require any special tooling for individual parts,” says Partlow. “Almost any geometrical shape can be constructed and it allows a part to be built that could not be made using current techniques.”
The process makes “near” net shape parts because it’s not possible to make the parts exactly how a manufacturer wants them.
Hummel says that although this process will never replace conventional manufacturing techniques because it is too slow, the list of applications for LENS is endless.
“Let’s say you need a hip replacement,” says Hummel. “Currently, the surgeon would implant an off-the-shelf hip stem or go to a custom hip stem company where one would be made from a billet of material. In this case, the billet would be made oversize and machined down into the final shape. Using LENS, the hip stem could be ‘grown’ to fit just right and it could be made from titanium or stainless steel.”
Partlow is designing a load cell to measure the mass flow rate of the metal powders through the machine.
“This is an important parameter to keep track of since it has a significant effect on the properties of the part being made,” says Partlow. “It is also valuable in determining the efficiency of the entire process such as how much of the powdered metal is actually being melted and added to the final part.”
“I am quite sure that the system he is working on is going to work well,” says Hummel. “By the time Ben finishes this work, it will be published in a professional journal. So as an undergraduate Ben is going to be published. That’s impressive! He’s got great grades, a fantastic attitude, can work independently, and will have at least one publication.”
Partlow decided to participate in this research project because he wanted a challenge.
“In most classes there is a single answer for each problem asked,” says Partlow. “However, in research, there are no answers, which allows for greater creativity. I also enjoy the fact that research, and particularly this project, brings the information learned in multiple classes together, which forces me to think more, not simply plug numbers into equations.”
“This opportunity is one of the reasons I chose to come to Lafayette,” continues Partlow, who transferred to Lafayette in the fall from the United States Naval Academy. “Very few other schools would have undergraduates working on this type of research. All of the funding usually goes toward graduate students.”
Hummel says the research will help Partlow no matter what path he takes in the future and that graduate schools as well as industry will be interested in him.
“Ben is an outstanding student and one of the best I have ever had the privilege of working with,” says Hummel. “He is very self-motivated, so he can take a project and run with it. He is a terrific student and maintains an A average in his coursework. He is very good at taking what he has learned in the classroom and applying it to the research problem. In addition, he is good with his hands, which is always a benefit to an engineer. He has no problem digging into the LENS equipment to make modifications. He’ll be successful, no doubt.”
Most of Partlow’s extracurricular activities involve volunteering. He is part of the Adopt-A-Class program and helped write the curriculum this semester. He is a Big Brother for a local seventh-grader and volunteers at the Shawnee Success Academy.
This past summer, Partlow had an internship with the Whiting-Turner Contracting Company, a general contractor from Baltimore. He shadowed a project manager, helping to supervise construction of a $12 million laboratory building.
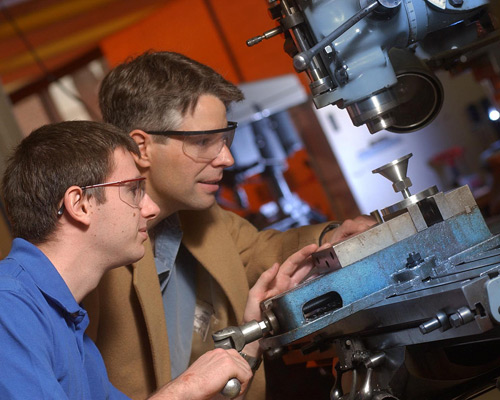
A National Leader in Undergraduate Research. Benjamin Partlow ’03 coauthored articles on his collaborative research with Scott Hummel, associate professor of mechanical engineering, in Wear and Tribology International.
1 Comment
Comments are closed.