By Bryan Hay
It’s a sticky challenge for Clark Addis ’20 to come up with a safer, more sustainable wood glue, but he looks to plants for a possible solution.
Particleboard, fiberboard, and plywood have traditionally been made with petroleum-based adhesives that pose health risks. When the wood eventually decays, the toxic synthetic glue lingers.
“The problem with current wood composites is that the wood is biodegradable, but the glue in them are not,” says Addis (mechanical engineering and art). “So we’re trying to make a bio-based glue that could be biodegradable, so when the wood is thrown away, the glue can decompose too.”
The objective for Addis and his adviser, Melissa Gordon ’11, assistant professor of chemical engineering (and previously Rachel Koh, then assistant professor of mechanical engineering), is to create a bio-based wood adhesive to reduce health risks and reliance on petroleum. Addis says his inspiration to study an alternative glue came from Koh’s research in discovering new ways to use biomaterials that are renewable and can be harvested in Pennsylvania, such as wood, hemp, and flax, and Gordon’s work with polymers.
Gordon says her research found that a linseed oil-based glue from flax showed great promise. In its raw form, before a chemical reaction modifies the oil into an adhesive, the gooey substance resembles raw honey in appearance and texture. The glue itself sets up in only about 10 minutes.
“It’s highly viscous and super sticky,” Addis says as he pulls strands of the substance out of a plastic dish using a small stainless steel spatula.
He tested the glue’s response under wet conditions on domino-sized pieces of Douglas fir, ash, and poplar, all common woods used in the construction industry. The glue seems to respond particularly well on poplar, perhaps because it’s less porous than other woods.
He also checked the glue’s strength in a tensile tester. It took a half a kilonewton for the locking, glued pieces of ash to fail.
Addis says plant-based glues, particularly soy-based glues, were once common until petroleum-based adhesives replaced them after World War I. With a renewed demand for nontoxic products, the time is ripe to return to natural raw materials and refine the processes to produce a safer glue.
“One problem with current bio-based adhesives is that they have poor moisture resistance and can’t withstand exposure to the weather,” he notes.
Polyurethanes show promise—they can be made using sugars, or even algae, and are non-carcinogenic, fast-curing, and water-resistant—but they can trigger an allergic reaction when manufactured.
Linseed oil, which is 100 percent bio-based, seems to have much potential. As an ingredient in glue, it forms a strong covalent bond and is non-carcinogenic.
“Hopefully this research will one day lead to wood-based construction and building materials that support a more sustainable future,” Addis says.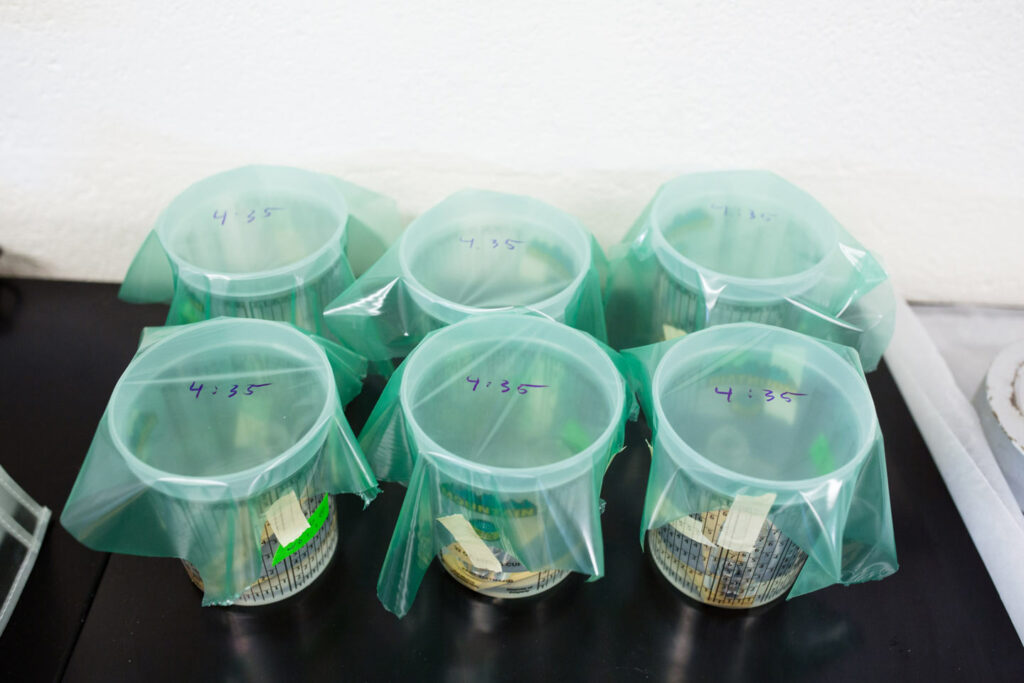